工場の危険予知・KY活動・ヒヤリハット対策まとめ!
監視カメラでできる安全対策
「工場内のKY活動がうまく機能していない気がする」
「事故やヒヤリハットを減らす具体策が知りたい」
工場・倉庫では労災事故やヒヤリハットを減らす安全対策が必要です。
危険予知(KY活動)が不十分だと、重大な事故につながるリスクは高まります。
しかし、ポイントを押さえた対策を取れば、安全な現場づくりは可能です。
とくに注目されているのが、防犯カメラによる見える化対策です。
事故の兆候を可視化し、迅速な対応が可能になります。
この記事でわかること
- KY活動の基本とヒヤリハット事例
- 現場で使える危険予知ネタ10選
- 防犯・監視カメラを活用した最新の安全対策
工場における事故やトラブルを防ぐ安全対策をお考えの方は、ぜひ参考にしてください。
なお、防犯カメラの導入費用や設置までの期間が気になる方は、お気軽にご相談ください。ご不安やご希望に合わせて、最適なご提案をいたします。
そもそも、工場の危険予知(KYT)とは?
工場での安全管理に欠かせないのが「危険予知活動(KYT)」です。
日々の業務の中に潜むリスクを事前に洗い出し、事故や災害を未然に防ぐための取り組みです。
KYTは単なる形式的なミーティングではなく、現場で本当に起こり得る「ヒヤリ」とした瞬間を共有し、対策を話し合うことに価値があります。
また、ヒヤリハットや5S(整理・整頓・清掃・清潔・しつけ)と連動させることで、職場全体の安全意識も向上します。
ここで解説すること
- KYTの基本と目的をわかりやすく解説
- ヒヤリハットとKY活動の関係性とは?
- 5Sとの関連性と現場での活かし方
KYTの基本と目的をわかりやすく解説
防犯カメラを活用すれば、普段の作業を「見える化」し、思わぬリスクに気づけます。
危険予知トレーニング(KYT)は、作業前に起こりうる危険を想定し、事故を未然に防ぐための活動です。
なぜKYTが重要なのかというと、人は「慣れ」や「思い込み」でリスクを見落としやすいためです。経験豊富な作業員でも、注意を怠れば思わぬ事故につながります。
たとえば、フォークリフトの運転前に「死角に人がいないか」「荷物のバランスは取れているか」などをあらかじめ確認すると、事故の可能性を減らせます。
このようにKYTは、単なる形式的なチェックではなく、安全意識を高めるための重要な活動です。
ヒヤリハットとKY活動の関係性とは?
ヒヤリハットとKY活動(危険予知訓練)は、どちらも安全対策に密接に関わっています。
ヒヤリハットの考え方は、1931年にアメリカのハインリッヒ氏が提唱した「ハインリッヒの法則」に基づいています。
ハインリッヒの法則とは?
1件の重大事故の背景には、29件の軽微な事故と、さらに300件のヒヤリハット(ニアミス)があるとされる法則
参考:厚生労働省 職場の安全ガイド「ハインリッヒの法則(1:29:300の法則)」
つまり、大きな事故は日々の小さな異常の積み重ねで起こるということです。
KY活動を行う意味とは?
- 滑りやすい通路が転倒事故につながる
- 表示ミスや確認不足が操作ミスを招く
- 声かけの不足が連携ミスを引き起こす
ヒヤリハットをKY活動で共有し対策することで、事故を防ぐ現場づくりができます。
ヒヤリとした経験を軽視せず、事故の芽として扱うことが、KY活動を実効性のあるものにするポイントです。
5Sとの関連性と現場での活かし方
KYTを機能させるには、5S(整理・整頓・清掃・清潔・しつけ)の徹底が不可欠です。
現場が整っていれば、リスクに気づきやすくなり、KYTの精度も高まります。
5Sの要素 | KY活動への効果 |
---|---|
整理 | 不要物の排除により、危険物への接触リスク減少 |
整頓 | 必要な道具が定位置にあることで、作業効率と安全性UP |
清掃 | 異常の早期発見(オイル漏れ・破損など)に貢献 |
清潔 | 清掃状態の維持により、異常を見逃しにくくなる |
しつけ | ルールを守る習慣がKYTへの意識定着につながる |
5SとKYTは、安全な現場づくりにおいて両輪のような存在です。
片方だけに力を入れるのではなく、日々の現場改善と意識づけをセットで進めることが、事故ゼロへの近道となります。
現場でよくある事故・ヒヤリハット事例
工場では、些細な見落としが重大事故につながります。とくに多いのが、以下のようなヒヤリハット事例です。
ここで解説すること
- 挟まれ・巻き込まれ事故
- 転倒・転落による負傷
- 薬品や機械との接触トラブル
挟まれ・巻き込まれ事故のケースと防止策
工場でとくに多いのが、機械や搬送設備による挟まれ・巻き込まれ事故です。
原因の多くは「安全装置の無効化」や「点検中の誤作動」など、ルール無視や確認不足によるものです。
たとえば、コンベア清掃中にスイッチが入ってしまい、手を巻き込まれるケースがあります。
挟まれ・巻き込まれ事故を防止する対策例
- 作業前のスイッチ切断とタグアウトの徹底
- 安全装置を解除しない運用ルールの遵守
- KYTによる事前のリスク洗い出し
挟まれ事故は重大化しやすいため、「起こる前提」で対策しましょう。
転倒・転落の発生要因と注意点
転倒や転落事故は、工場内のあらゆる場所で発生しやすいリスクのひとつです。
主な原因は、「床の滑り」「段差の見落とし」「高所作業中のバランス崩れ」などがあります。
これらを防ぐには、以下のような対策が必要です。
転倒・転落事故を防止する対策例
- 床や通路の定期清掃・点検
- 高所作業時の安全帯の着用
- 作業前のKYTによる注意喚起
このように、事前の環境整備と意識づけがカギとなります。
薬品や機械との接触トラブルの実例
工場では、薬品や可動機械との接触によるトラブルも発生します。
薬品取り扱い時の「手袋未着用」や「目に入る飛散事故」、機械稼働中の「不用意な接近」などが代表例です。
たとえば、洗浄作業中に薬品が跳ねて目を負傷したケースもあります。
こうした事故を防ぐには、以下が効果的です。
薬品・機械との接触によるトラブルを防止する対策例
- 保護具の着用ルール徹底
- 作業範囲への明確な表示
- 接触リスクを想定したKYTの実施
基本を守ることが、重大事故の抑止につながります。
KY活動を活性化させるアイデア・例題10選
KYT(危険予知トレーニング)を形だけの活動にしないためには、現場に合ったリアルな例題を使うことがポイントです。
ここでは、工場現場で実際に起こりやすい10のリスクをもとに、KYTに活用できる例題を紹介します。
工場で対策しておきたいリスク
フォークリフト作業時の接触リスク
フォークリフトは、工場内での接触事故が起こりやすい作業です。
後進時や交差ポイントでは、死角にいた作業員と接触しかける「ヒヤリ」とした瞬間が多く報告されています。
フォークリフト作業時のよくあるヒヤリハット例と対策例
- 死角に作業員がいて、接触寸前まで気づかなかった
- 主な原因:死角による確認不足
- 対策例:カーブミラーの設置、誘導員の配置
- クラクションを鳴らさずに後進し、後方の人物が慌てて避けた
- 原因:クラクション未使用
- 対策例:発進・交差時のホーン使用をルール化
- 荷物で前方視界が遮られ、人や障害物に気づけなかった
- 通路が狭く、人と機械が交差しやすい
- 専用通路の確保、通路幅の見直し
KYTでは、「いつ・どこで・どのタイミングで人と接触する恐れがあるか」を具体的に洗い出すことが事故防止につながります。
重量物運搬中に手を挟まれる可能性
重量物の運搬中は、指や手を挟む事故が多発する高リスクな作業です。
重量物運搬中のよくあるヒヤリハット例と対策例
- 台車に重量物を載せる際、手を挟みかけた
- 主な原因:持ち上げ・設置時の連携不足
- 対策例:作業前に声かけ・手順確認を徹底
- 持ち上げるタイミングがずれ、仲間の指を圧迫しそうになった
- 原因:手の置き場所のルールが曖昧
- 対策例:安全な持ち方・持つ位置をKYTで共有
- 手の位置が不安定で、荷物の下敷きになりそうになった
- 原因:無理な体勢・一人作業での持ち上げ
- 対策例:二人以上で作業、専用リフターや台車を活用
KYTでは、「どの瞬間に手が危ないか」「どうすれば巻き込まれないか」を想定し、声かけや持ち方まで共有しておくことが効果的です。
脚立作業中の転倒・バランス崩れ
脚立を使った作業では、ちょっとした油断が転倒やケガにつながるリスクがあります。
脚立作業中のよくあるヒヤリハット例と対策例
- 脚立を完全に開かずに使い、作業中にぐらついた
- 主な原因:設置不良や固定せずに使用
- 対策例:水平で安定した場所に完全に開いて設置
- 工具を片手に持って脚立を昇降し、バランスを崩した
- 原因:両手がふさがった状態での作業
- 対策例:工具は腰袋へ、昇降時は両手を空ける
- 足場の不安定な場所に脚立を立て、横転しかけた
- 原因:高所作業のルールがあいまい
- 対策例:高さ制限・安全帯使用の明確化
脚立作業では、「事前の設置チェック」「道具の持ち方」「周囲の確認」が事故防止のポイントです。KYTで注意点を共有することで、安全意識が高まります。
薬品取り扱い中の皮膚・目への接触
薬品を扱う作業では、皮膚への付着や目に入るリスクがつきまいます。
製造過程についても十分に注意をはらう必要があります。
薬品取り扱い時のよくあるヒヤリハット例と対策例
- ゴーグルをつけずに薬品を開封し、飛沫が顔にかかった
- 主な原因:保護具の不使用
- 対策例:ゴーグル・手袋・エプロンの着用徹底
- 手袋をせずに作業し、皮膚が赤くただれた
- 原因:手順の省略や慣れによる油断
- 対策例:毎回KYTで作業手順と注意点を復習
- 薬品をこぼし、床が滑りやすくなっていたことに気づかなかった
- 原因:こぼれ対応ルールが曖昧
- 対策例:「即拭き取り・報告・注意喚起」の徹底
KYTでは、「作業中に誰かが誤って操作する可能性があるか?」をテーマに、役割や連携方法まで具体的に確認しておくことが事故防止につながります。
機械メンテナンス中の誤起動事故
機械の点検や清掃中に誤って電源が入り、作業者が巻き込まれそうになる事故は後を絶ちません。
機械メンテナンス時のよくあるヒヤリハット例と対策例
- 点検中に他の作業者が操作盤を誤って作動させそうになった
- 主な原因:電源を完全に落としていなかった
- 対策例:ロックアウト・タグアウトを徹底
- 電源を切ったつもりが、補助スイッチが入っていた
- 原因:警告表示や作業中サインが不十分
- 対策例:「操作禁止」表示を目立つ場所に貼付
- 誰かが機械を動かそうとして、警告表示に気づかなかった
- 原因:作業中の情報共有が不十分
- 対策例:点検前後の声かけ・チェックリストの運用
KYTでは、「作業中に誰かが誤って操作する可能性があるか?」をテーマに、役割や連携方法まで具体的に確認しておくことが事故防止につながります。
作業通路に置かれた資材でのつまずき事故
作業通路に資材や工具が置かれていると、つまずきや転倒による事故が発生しやすくなります。
通路上のヒヤリハット例と対策例
- 段ボール箱に足を引っかけて転倒しそうになった
- 主な原因:仮置きスペースと通路の区別が曖昧
- 対策例:通路と置き場の明確な区分と表示
- 通路に置かれた工具が視界に入らず、つまずいてよろけた
- 原因:忙しさによる一時的な置き忘れ
- 対策例:KYTで「置きっぱなしのリスク」意識づけ
- 資材の仮置きが繰り返され、常態化していた
- 原因:点検や清掃の頻度が不足している
- 対策例:通路チェックを日常業務としてルーティン化
KYTでは、「どこに物が置かれやすいか」「誰がどう片づけるか」を具体的に話し合い、通路は常に空けておくという安全文化を育てましょう。
⑦ 確認ミスによる誤操作(スイッチ・バルブ等)
スイッチやバルブの操作ミスは、ヒューマンエラーによる典型的なトラブルです。
誤操作によるヒヤリハット例と対策例
- 冷却バルブと排出バルブを間違えて操作し、液体があふれそうになった
- 主な原因:スイッチやバルブの表示が不明瞭
- 対策例:ラベル貼付・色分けによる識別
- 非稼働中のスイッチを誤って押し、装置が急に動き出した
- 原因:操作前の確認が不十分
- 対策例:指差し呼称・ダブルチェックの習慣化
- 「誰かが確認したと思い込んで」操作した結果、誤動作が発生
- 原因:作業の役割分担が曖昧
- 対策例:操作担当の明確化と複数人確認
KYTでは、「どのスイッチ・バルブが紛らわしいか」「どのタイミングでミスが起きやすいか」を洗い出し、確認ミスによる事故の芽を事前に摘みます。
作業員の慣れによる省略行動
作業に慣れてくると「大丈夫だろう」という油断が増え、事故のリスクが高まります。
慣れによる省略行動のヒヤリハット例と対策例
- 高所作業で「ちょっとだけ」と安全帯を着けずに作業した
- 主な原因:繰り返し作業による油断
- 対策例:「慣れこそリスク」とKYTで共有
- 点検を省略して機械を運転し、異音に気づくのが遅れた
- 原因:安全手順が軽視されている
- 対策例:作業手順書の見直しと安全教育
- 足元確認を省いた結果、小さな段差でつまずいた
- 原因:ベテランへの注意がしづらい雰囲気
- 対策例:フラットな職場づくりと声かけ促進
KYTでは、「この作業、慣れてきたからこそ注意が必要では?」と問いかける視点を取り入れることで、省略行動の防止につながります。
複数作業者の連携不足による危険行動
連携ミスによる事故は、思い込みや確認不足が原因になるケースが多いです。
連携不足によるヒヤリハット例と対策例
- 作業の引き継ぎが曖昧で、前の工程が完了していなかった
- 主な原因:声かけや手順確認が不足
- 対策例:作業前・中・後の声出し確認をルール化
- 合図を待たずに工具を動かし、飛びそうになった
- 原因:作業の順序や役割が曖昧
- 対策例:役割分担と手順をKYTで共有
- 重要なチェックを誰もしていなかった
- 原因:暗黙の了解で作業が進んでいた
- 対策例:「思い込み禁止」の意識づけを徹底
KYTでは、「誰が・いつ・どの作業をするか」「何を合図に動くか」といった細かな段取りまで話し合うことで、チーム内のミスを防げます。
安全確認を怠った搬入作業での衝突
搬入・搬出時は人や車両の動線が交差しやすく、衝突リスクが高まります。
搬入時の衝突に関するヒヤリハット例と対策例
- トラックの後退時に作業員と接触しかけた
- 主な原因:後方確認や誘導が不十分
- 対策例:誘導員配置、「声かけ・目視」の徹底
- 搬入中に人が横切り、荷台が接触しそうになった
- 原因:作業エリアと通行動線が重なっていた
- 対策例:歩行ルートと車両ルートの明確な分離
- フォークリフトと台車が同じ通路でぶつかりかけた
- 原因:作業スピード優先の風潮
- 対策例:「安全第一」を徹底し、スケジュールを見直す
KYTでは、「どの動線で誰が動くか」「視認性が悪い場所はどこか」を具体的に洗い出すことで、搬入時の衝突を未然に防ぐ意識を高められます。
工場向けの監視カメラって?料金は?まずは無料で相談
防犯・監視カメラが危険予知対策に効果的
KYT(危険予知トレーニング)で近年注目されているのが、防犯カメラを活用した「見える化」による危険予知対策です。
ここでは、防犯カメラを具体的にどう活用できるのか、4つの視点から解説していきます。
ここで解説すること
- 日常作業を可視化し、リスクを発見しやすくする
- 異常のあと追いができるトレーサビリティの強化
- 転倒などの異常行動を即時検知し、迅速対応を実現
- 不審者や立入禁止区域への侵入をリアルタイムで検知
日常作業を可視化し、リスクを発見しやすくする
防犯カメラを活用すれば、普段の作業を「見える化」し、思わぬリスクに気づけます。
人の記憶や感覚だけでは見逃されがちな危険も、映像で客観的に確認できるのがメリットです。
たとえば、いつの間にか省略されていた安全確認や、無意識のうちにルール違反になっていた動作も、映像を見て気づくことがあります。
防犯・監視カメラで可視化できるリスクの例
- クラクションを鳴らさずに進むフォークリフト
- 脚立の不安定な使い方が習慣化していた
- 資材を通路に一時置きし、それが常態化していた
当たり前になっていた危険に気づけることで、KYT活動のテーマも具体的になり、現場の安全意識が高まります。
異常のあと追いができるトレーサビリティの強化
防犯カメラを設置しておくことで、記録を正確に残せるため、異常やトラブル発生時の「あと追い」ができる体制が整います。
たとえば、「いつ誰がどんな操作をしたか」や「どこで危険な動きがあったか」などの状況を、監視カメラの録画データがあれば正確に振り返ることができ、その後の対応に役立ちます。
トレーサビリティが活きる場面の例
- 作業ミスのタイミングと原因を特定したいとき
- クレーム対応や報告書作成で客観的な証拠が必要なとき
- KY活動で過去事例を再活用したいとき
トレーサビリティを強化することで、「その場しのぎ」ではない改善活動ができます。
転倒などの異常を即時検知し、迅速対応を実現
防犯カメラの中でもAI機能を備えたモデルを活用すれば、転倒や異常動作をリアルタイムで検知し、即座に対応可能です。
転倒検知AIが工場のKYTに役立つ例
- 一人での夜間作業中、作業員が資材につまずき転倒した
- 機械の整備中に体調を崩して倒れ、そのまま気づかれずにいた
- 高所作業中にバランスを崩して着地に失敗、動けなくなった
これらのケースでは、AIカメラが「倒れた動作」を検知し、関係者へ即通知することで「誰も見ていなくて気付かなかった」という事態を防ぎ、迅速な対応が可能になります。
不審者や立入禁止区域への侵入をリアルタイムで検知
防犯カメラのAI機能を活用すれば、工場内への不審者の侵入や、立入禁止区域への誤進入をリアルタイムで検知できます。
工場のKYTで侵入検知AIが役立つ例
- 外部業者が誘導ミスで危険区域に入りそうになった
- 高電圧設備エリアに新人が誤って立ち入った
- 深夜帯に外部から不審な人物が敷地内に侵入した
こうした場面でAIカメラが即時に侵入を検知すれば、管理者がすぐに現場へ駆けつけ、事故やトラブルを防止できます。
AIカメラを活用して、工場の危険予知を行いたいと考えている方は、ぜひお気軽にお問い合わせください。
現地調査・お見積り無料!
トリニティーで工場に防犯カメラを導入するメリット
トリニティーは、現場の課題やニーズに寄り添ったカメラ導入を支援することで、
導入から運用・アフターサポートまで、ワンストップで現場の安全強化をサポートします。
ここでは、トリニティーで導入する3つのメリットを紹介します。
ここで解説すること
- レンタルで初期費用0円で導入
- 工場の製造現場向けの、最善の監視カメラをご提案
- アフターフォローで安心
レンタルで初期費用0円で導入
「防犯カメラの導入は高そう…」
そう感じて踏みとどまっている方も多いかもしれません。
トリニティーなら、工場向けの業務用監視カメラをレンタル、リース、一括買取にてご利用いただくことができます。
特にレンタルは、初期費用0円の月額定額料金のみでお使いいただいけるため、「コストを抑えたい」「経費管理を簡単にしたい」という工場でもおすすめです。
工場で業務用防犯カメラをレンタル導入するメリット
- 初期費用0円で導入できる
- 月額制で費用を計算しやすい
- 契約期間に応じた柔軟なプランで導入しやすい
「安全対策を強化したい。でも大きな投資は避けたい」
そんな現場に、トリニティーのレンタルサービスは最適な選択肢です。
工場の製造現場向けの、最善の監視カメラをご提案
せっかくカメラを設置しても、死角があったり、映像が不鮮明だったりすると、本来の効果を発揮できません。
だからこそ、専門業者はお客様一人一人に合わせてカメラシステムをカスタマイズします。
トリニティーでは、現地調査を無料で行い、工場の構造やエリアに応じて、最適な機種・設置場所をご提案します。
工場向け監視カメラの例
- リスクの高いエリア(立入禁止区域、危険物周辺など)をカバーするAIカメラ
- 夜間の盗難被害防止のための夜間対応カメラ
- 防爆エリア対応の防爆カメラ
- オイルミストなど、製造ラインのさまざまな環境に耐える防塵防水性能の高いカメラ
監視カメラを活用して工場のKY活動、安全対策を強化したい場合は、ぜひ弊社トリニティーにお任せください。
長期保証で安心
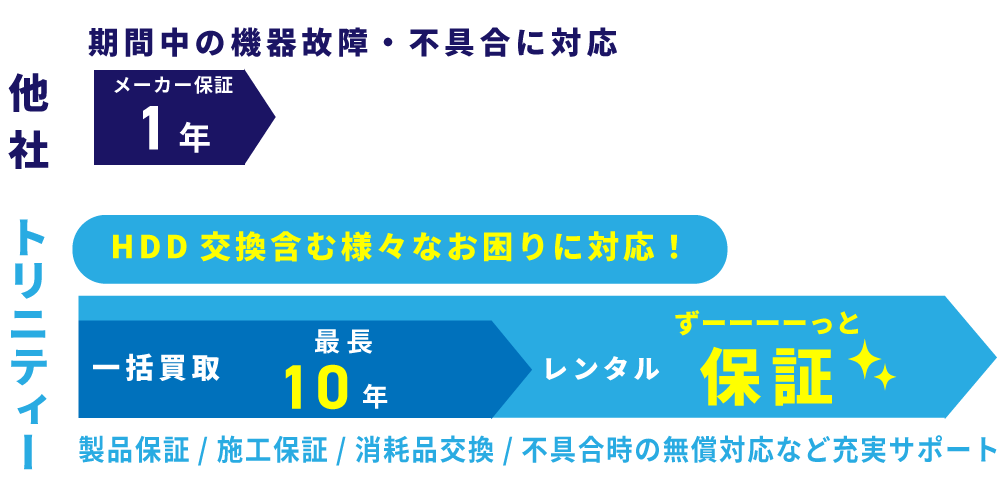
防犯カメラは、導入後のトラブル対応やメンテナンスのしやすさもポイントです。
トリニティーでは、レンタル中の機器に保証がついており、故障や不具合が発生した場合も安心して利用できます。
カメラ本体だけでなく、HDDなどの消耗品も対象です。万が一の際には出張修理にも対応しており、現場での業務を止めずにすぐ復旧できます。
機器の選定から設置工事、アフターフォローまで一括して対応できるので、安心して防犯カメラを設置できます。
防犯カメラを工場に導入し、危険予知に活かしたい方は、ぜひ一度ご相談ください。
現地調査・お見積り無料!
工場の危険予知活動でよくある質問
最後に工場の危険予知活動でよくある質問について紹介します。
- 工場の危険予知活動は義務ですか?
-
工場での危険予知活動は、法律で明確に義務付けられているわけではありません。
しかし、労働安全衛生法第24条では、労働災害を防止するために事業者が必要な措置を講じることが求められています。このため、危険予知活動は労働災害防止の一環として、積極的に取り組むことが望まれています。
- 安全基本4行動とは何ですか?
- 以下の4つが一般的な「安全基本4行動」です。
- 指差呼称(しさこしょう)
- 足元確認
- 手順遵守(てじゅんじゅんしゅ)
- 声かけ・報告
- 工場での安全5原則は何ですか?
- 工場などの作業現場では、「安全5原則」が安全管理の基本とされており、5Sとも呼ばれています。
以下が代表的な5つの原則です。
- 整理
- 整頓
- 清掃
- 清潔
- しつけ
- ヒヤリハットと危険予知の違いは何ですか?
- ヒヤリハットは「過去から学ぶ」安全活動、危険予知は「未来を見通す」安全活動です。
両方を組み合わせることで、より効果的に労働災害を防止できます。
監視カメラでセキュリティもKY活動も両立
工場のKYT(危険予知トレーニング)を形だけで終わらせず、本当に事故を防げる仕組みにするためには、見える化の工夫が欠かせません。
その手段として、防犯カメラの活用は非常に有効です。日常のリスクを可視化し、異常を即時に検知し、原因もあとから追及できます。
トリニティーの防犯カメラなら、コスト負担を抑えつつ、現場に合わせた提案・サポートも万全です。KYTの強化と現場の安全性アップを、同時に実現できます。
「安全対策を続けられる形に変えたい」
そうお考えの方は、防犯カメラの導入を検討してみてください。
現地調査は無料で行っております。ぜひお気軽にお問い合わせください。
工場・倉庫向け防犯カメラ特設ページ
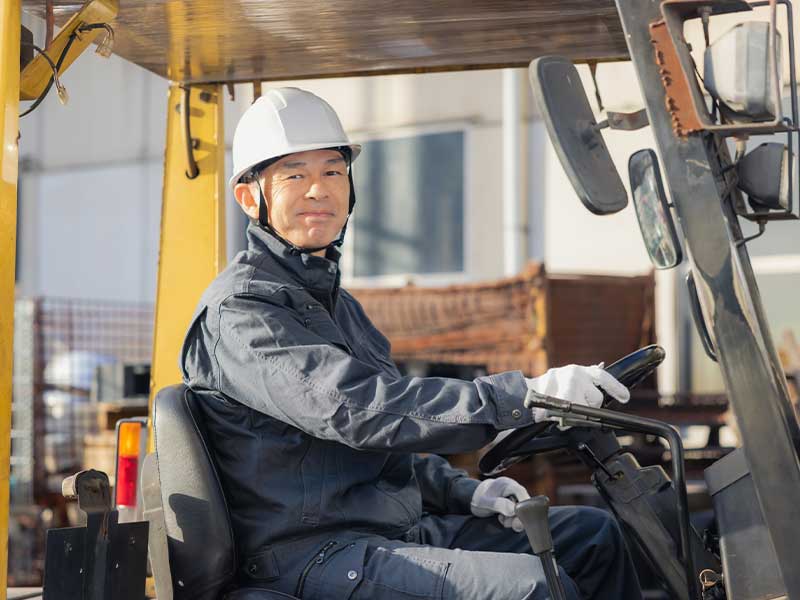
工場・倉庫では金属や重機の盗難を防ぐセキュリティ対策や、異物混入や労災事故を防ぐためのリスク対策が必要不可欠です。
トリニティーではそんな製造ラインのお悩みを解決する数々のソリューションを展開しています。
スタンダードな監視カメラシステムから現場のDX・省人化を推進するAIカメラシステムまで、お気軽にご相談ください。
詳細はこちら